Not a particularly complex project. But it made something "not so useful" into "way more useful". Just wish I had a stouter bandsaw to work with.
Have a Greenerd #30 3-ton arbor press which was originally designed for elec motor repair. Pressing armatures off, bearings, etc. Got it from HGR pretty cheaply as it had fallen over and broken the racheting mechanism into a bunch of pieces. I just wanted the stand for my Greenerd #3 that didn't have a stand, but took it all. The stand, press frame, & ram were still all good, all else being broken to pieces. After ebay searching found a cheap hacked up 3T arbor press for cheap BIN price that had a good donor pinion I could use to make it operable as non-racheting. Good thing about this is the huge amount of daylight it offers, at 18" capacity.
It came with an 11 x 12 x 3/8 thick plate attached to it which wasn't useful in many cases in that configuration. So I cut the plate down, drilled a sequence of holes up to 1 inch diam as that was the biggest drill I had. Then w/ boring head upped the diameter to 2-1/8. Then rough band-sawed the hole to make it a slot. Then finished all on the the Bridgeport to clean up the saw-cut surfaces. Ground the corner radii w/ a belt sander.
All in all it was like 32 inches of sawing on a Delta-Rockwell 14" wood/metal bandsaw. All total it took well over an hour+ of sawing. Used a 4T blade and let it do all the work. But I don't know how I could have done the cutting any faster on such a light-duty saw? My hand and wrist were definitely feeling that effort.
Pretty happy how it came out. Was thinking the 3/8 plate might flex under load but seems fine w/ my 148 Lbs hanging off the end of that press lever.
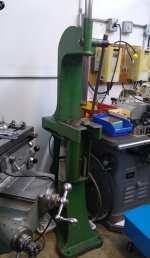